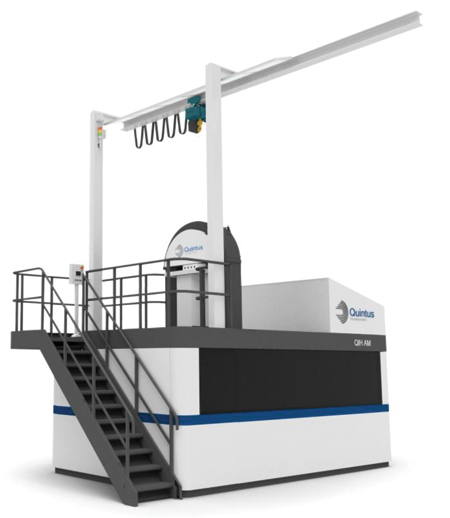
With a workload capacity of 600 kg (1,322 lbs.), model QIH 60 M URC combines heat treatment and cooling in a single process (HPHT).
Quintus Technologies offers a Hot Isostatic Press (HIP) that is designed to accelerate the additive manufacturing (AM) process by reducing the number of steps in the production line. Equipped with Quintus' proprietary Uniform Rapid Cooling, model QIH 60 M URC combines heat treatment and cooling in a single process known as High Pressure Heat Treatment (HPHT) for faster throughput, higher workpiece quality, lower capital investment and logistics costs, and increased energy savings.
"HIP has become the standard method to eliminate pores and remove internal defects in metal and ceramic parts, improving properties such as toughness and fatigue life," said a company spokesperson. "With the ability to stress relieve, heat treat and age parts in one system, Quintus HPHT allows manufacturers to consolidate several steps and remove discrete equipment from the production line. It is rapidly emerging as the go-to post-processing path to lean AM operations."
Equipped with digital controls for precise heating and cooling performance, the press has been designed to integrate with Industry 4.0 and factory of the future connectivity. The QIH 60 operates at a maximum temperature of 1,400 °C (2,552 °F) and pressure of 30,000 PSI (2,070 bar) when using the molybdenum furnace. Graphite furnace options are also available for temperatures up to 2,000 °C (3,632 °F). The working dimensions of the vessel are 410 mm (16.14") in diameter and 1,000 mm (39.37") in height, with a capacity of 600 kg (1,322 lbs.) per load, allowing loading of full build plates from the majority of printers.
"The innovative wire-winding technology introduced by Quintus is engineered to be a reliable and durable pressure containment system," said the spokesperson. Completely documented quality systems govern all phases of the production process and comply fully with ASME U3 and CE (PED) quality standards.
"Active controlled cooling facilitates stress relief, hot isostatic pressing, quenching and aging in the same HIP system with higher productivity," said the spokesperson. "This capability makes the QIH 60 M URC especially well-suited for materials that require rapid cooling or quenching after annealing, decreasing lead times and often eliminating the need for outsourced treatments."
"HPHT introduces multiple efficiencies and dramatically lowers per-unit processing costs," said Jan Söderström, CEO, Quintus Technologies. "We are very pleased with the role this state-of-the-art HIP can play in moving additive manufacturing forward into robust, lean production."
For more information contact:
Quintus Technologies LLC
8270 Green Meadows Drive N
Lewis Center, OH 43035
614-891-2732
info@quintusteam.com
www.quintustechnologies.com