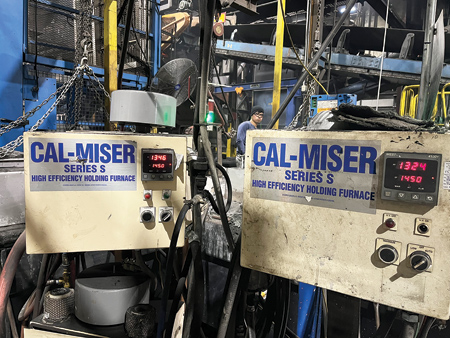
LeClaire uses state-of-the-art furnaces for near constant production within its aluminum die casting production facility.
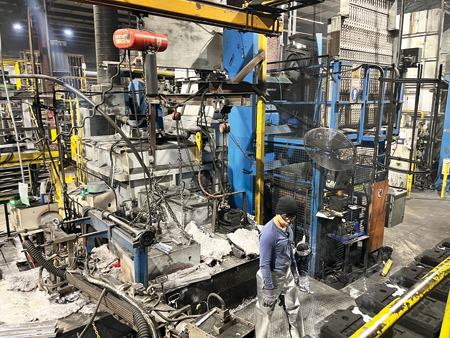
Operating environments of the CADDIS Machine Monitoring System include all manner of heat and chemistry encountered in today's manufacturing operations.
No need for a meltdown-or a "freeze up," as the case would have been for LeClaire Manufacturing when a critical furnace failed within its aluminum die casting operations. These workhorse furnaces run almost continuously in foundry operations providing performance, energy savings and reliability. Until they do not.
Sometimes those reliable pieces of equipment develop mechanical or electrical problems that go unnoticed, but a failure alarm did not.
"At that moment, a text message was sent by the CADDIS System to our foreman and action was taken immediately that saved our bacon," said Ralph Zimmerman, LeClaire Manufacturing Co-President. "We were able to intervene in literally a matter of seconds after the unit overheated and shut off."
If not addressed, what happens next is nothing short of a disaster. After a furnace failure, the unit shuts off and the front of furnace bath freezes, causing a cascading effect of failures. Tallying this up is daunting. It starts with a lot of specialized labor to unfreeze the front of the furnace, estimated at $8,000 to $10,000. The next step is to save the metal pump, which itself is a $20,000 unit. Then it is the inspection of the lining of the furnace to determine whether it had been damaged-a process that is very difficult to accomplish. Even fuel costs, for example to melt the metal, are part of the equation. But perhaps the biggest cost is downtime and resulting missed customer orders.
There is An Upside
In this case, all of these subsequent catastrophic failures were avoided due to the continuous CADDIS System. There was also no delay with the subsequent processes that LeClaire performs for its customers. After the parts have been cast, they are heat treated, machined to customer specification and delivered. LeCalire has CADDIS installed on numerous presses where they track uptime, downtime, maintenance tasks as well as shifts and other key metrics.
What Is CADDIS?
CADDIS is a two-pronged Industry 4.0 solution that uses a shop floor device and an intuitive software platform. The device is housed in a durable and sealed aluminum casting and is designed to work without interruption in even the harshest environments. It connects to any type or vintage of machine relaying user specified data to a central dashboard. That dashboard is the brain of the operation, providing real-time monitoring for continuous observation, improvement and intervention. The results are increases in uptime, improved Overall Equipment Effectiveness (OEE), predictive maintenance intervals and, most notably in this case, avoiding downtime, repair, scrap and missed customer deliveries.
"It is pretty impressive when you stop and think about it. We were in the middle of our shift thinking all was running perfectly, and then we got a text from the CADDIS system," said Zimmerman. "We were able to contain the failure right away and avoid what would have very rapidly become a next-level costly issue."
For more information contact:
CADDIS Systems
2727 62nd Street Ct.
Bettendorf, IA 52722
563-551-6418
www.cadissystems.com
LeClaire Manufacturing
3225 Zimmerman Drive
Bettendorf, IA 52722
563-723-0424
www.leclairemfg.com