




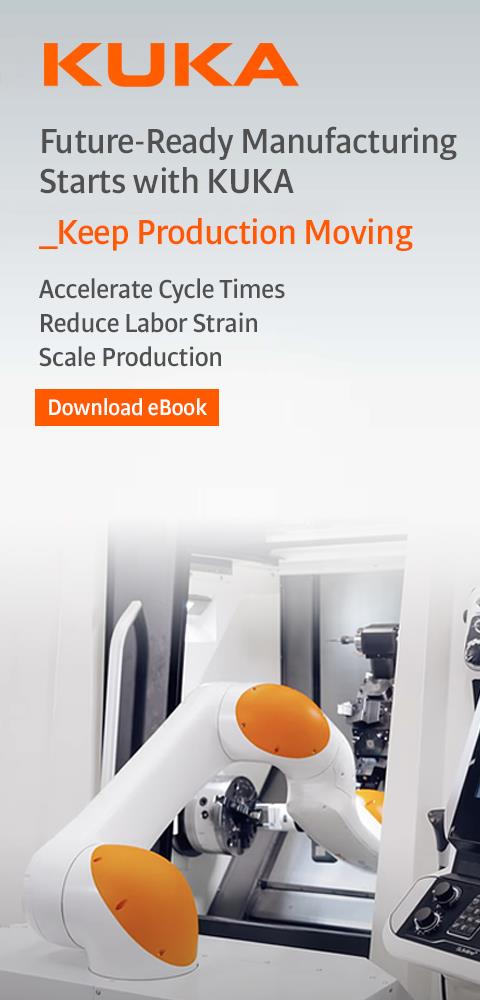
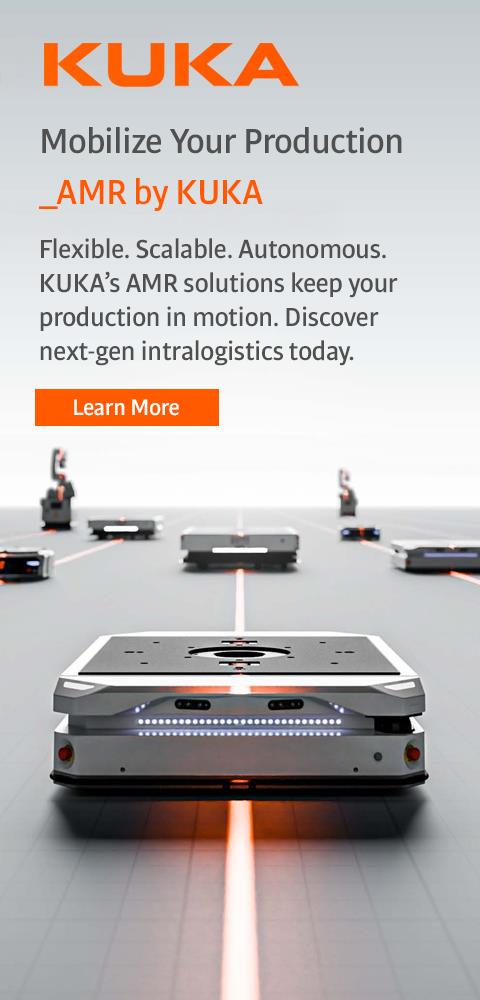
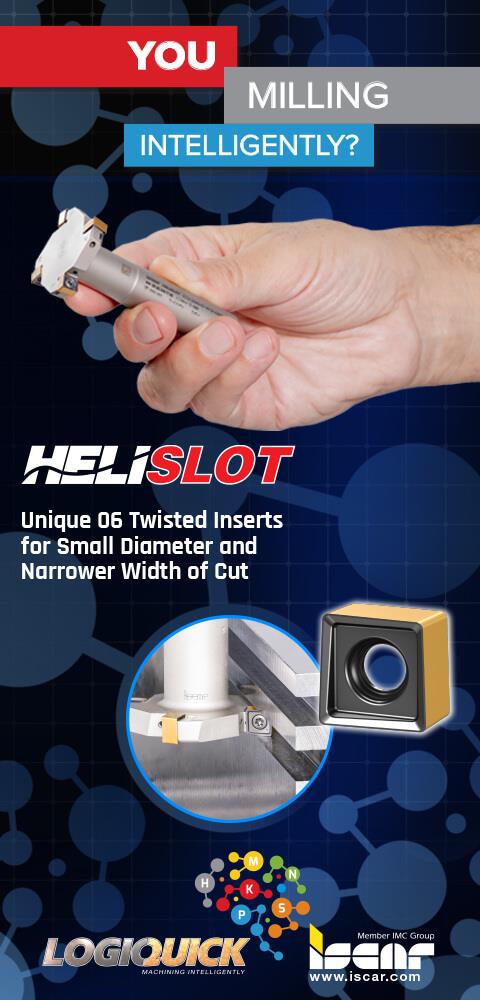
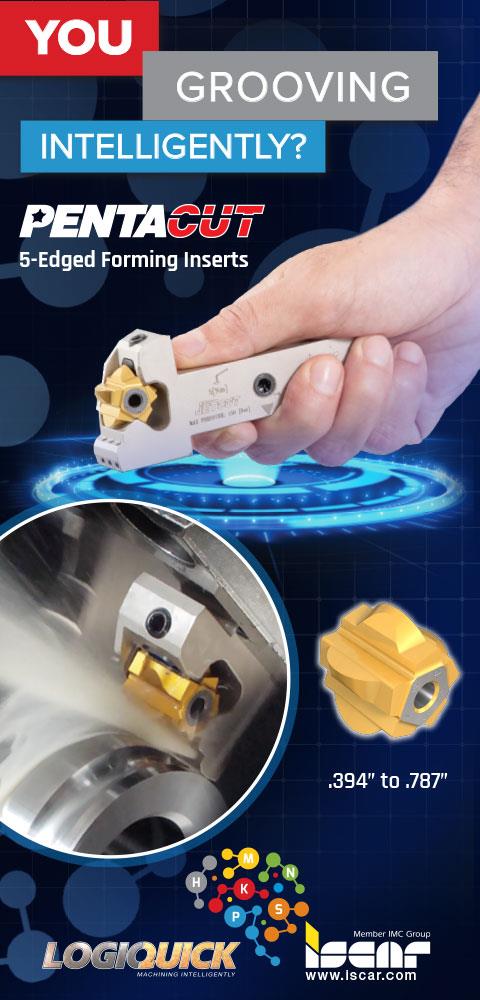
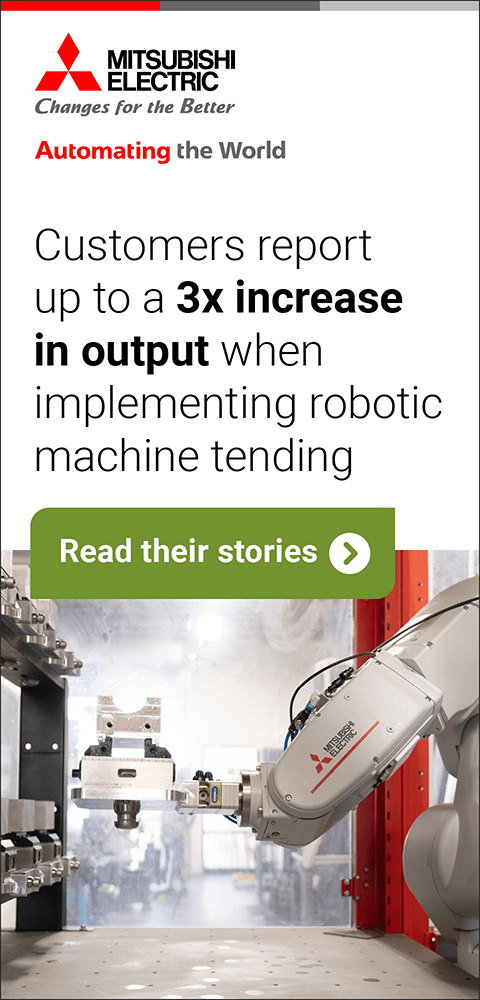
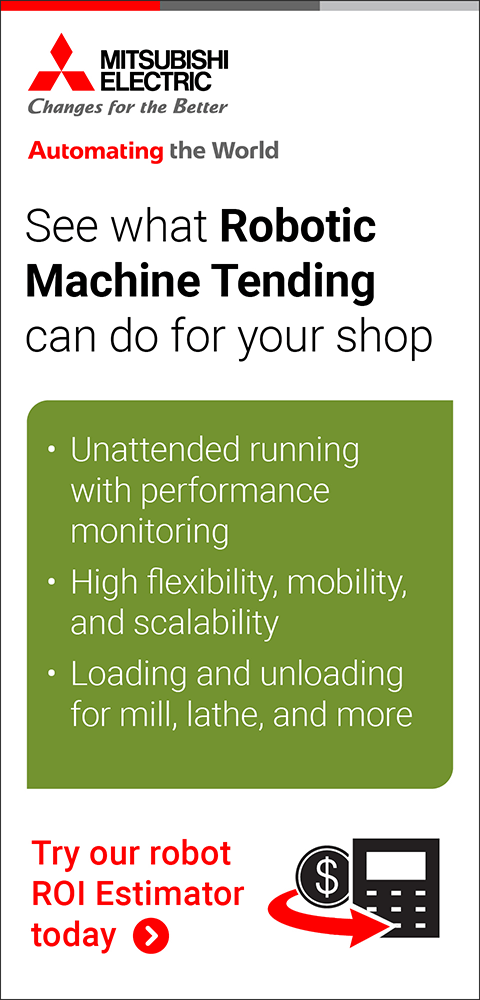
Compact Solution for Grinding Complex Geometries
August 1, 2019
The MFP 30 5-axis grinding center from MÄGERLE is suited for grinding complex geometries, particularly those of blades and vanes or heat shields for aircraft turbines. The workpieces to be machined can be loaded into the work area ergonomically, either manually or automatically. "The compact and space-saving design allows optimal use of the available production area and enables an effective production flow," said a company spokesperson.
For highly flexible workpiece machining, the integrated tool changer can be loaded with different grinding wheels, tools for milling and drilling operations and a measuring probe for quality or workpiece position checks.
"The powerful spindle drive enables different grinding processes to be combined, such as creep feed grinding with corundum or grinding with CBN," said a company spokesperson. "The full performance and a high torque are available even at low speeds. The robust toolholding fixtures enable wide machining contours to be achieved, together with high removal rates. The grinding process can use emulsion or oil. The high speeds of the high-performance spindle of up to 12,000 RPM offer optimal machining conditions for demanding grinding and milling processes, which are carried out in the same clamping."
The grinding process is optimized with the grinding wheel cleaning function. "The grinding wheel remains clean and sharp for longer periods during the grinding process, contributing to a higher stock removal rate with reduced grinding wheel wear," said the spokesperson.
The table dressing device can take wide diamond rolls with a large variety of machining profiles for different workpieces, minimizing set-up times. The modern drive technology enables reliable dressing across the entire speed range.
For more information contact:
UNITED GRINDING North America Inc.
2100 UNITED GRINDING Blvd.
Miamisburg, OH 45342
937-859-1975
info@grinding.com
www.grinding.com
< back