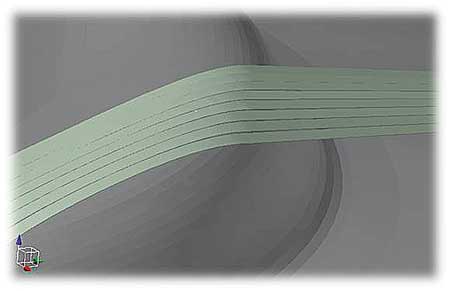
Simulation of composite material laying.
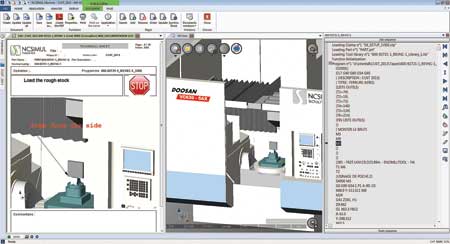
Create and synchronize documentation in just a few clicks.
SPRING Technologies has announced the latest version of NCSIMUL Machine 9.1, its flagship machining simulation software. Highlights include simulation of composite material laying, complete integration of the NCdoc document publication module and automated functions to enhance user experience.
Simulation of Composite Material Laying
NCSIMUL Machine 9.1 makes it possible to replicate material laying processes executed by numerical control (NC) machines. Just as it does in conventional machining, NCSIMUL Machine 9.1 decodes all types of NC programs, representing the complete machine environment in 3D to identify and analyze programming errors and collisions. The "Composite" option of this version also enables a dynamic representation of fiber ribbon laying, taking into consideration the 3D form of the carbon fiber. The positioning of each fiber in the ribbon is managed independently.
NCSIMUL Machine 9.1 alerts users to issues that are specific to the way composites are processed and that are liable to occur on real-world machines. These include fiber steering angle errors generating possible deviation; twisting of taut fiber between the head and the position on the spool; fiber tension issues including speed disparities between fibers or sudden changes of direction creating backwards laying.
Analysis functions can be used to communicate information to the process planning department and the design office before going live. This includes the length of the laid material, layer thickness measurement, fiber ribbon intersection angle, aperture radius, etc. The section plane function gives insights into layering or possible holes in the material. At any time, users can export the fiber path or the end result of the material laying generated on the tooling in CAD format.
NCSIMUL Machine 9.1 takes into consideration the shape of the initial tooling and the tension applied to the fibers. SPRING Technologies has developed new algorithms enabling fiber laying simulation with performances of 300 m/min. on a conventional CAD workstation.
All the functions dedicated to composite technology are grouped together in a new ribbon (Office mode) for a fast and effective learning curve.
Creation / Synchronization of Documentation
The NCdoc add-on is now fully integrated into NCSIMUL Machine 9.1. As for the Composite option, the technical content publication functions are accessed via a specific ribbon in the software's MMI. In just a few clicks users can create a set of documents for the shop floor from machining simulation information (tool sheets with associated times, tooling assembly sheets, machining results between operations, internal check sheets, etc.). The pages can be edited: by right-clicking, users can insert the 3D view of the machining in the document, while markup functions are also accessible to enrich the document if required before exporting the document in PDF or HTML format.
With NCSIMUL Machine 9.1, users can also link a page in the document set to an NC program block. A project exported in NP3 format now encapsulates the associated document, maintaining the links between pages and blocks. The NC operator viewing the simulation can use the free viewer, NCSIMUL Player 9.1, to bring relevant information up on the screen while displaying the simulation.
New Features
Automatic saving of intermediary rough stocks saves time, notably on programs that involve multiple machining operations. Intermediary rough stocks produced during a simulation are saved automatically at each tool, program or sub-program change. This makes it possible to replay the simulation from the latest valid rough stock before the detection of an error (collision, alert, etc.) or a change, without having to start over.
Automatic removal of support lugs from the rough stock at the end of the simulation has been added. NCSIMUL Machine 9.1 automatically recognizes support lug information in order to keep the simulated part and not the associated scrap.
NCSIMUL Machine 9.1 currently enables machine accessories to be positioned automatically by processing the contact with tailstocks, rests and chucks on the machined rough stock. The tailstock, for example, will be positioned alone, in contact with the machined rough stock. With this new feature, the rests are closed as soon as they touch the machined rough stock. This enables the job to be set up and built more quickly.
To facilitate data exchange, the latest version of NCSIMUL Machine 9.1 offers a new CAM interface with Alphacam 2013, in addition to the existing CAM interfaces.
For more information contact:
Silvre Proisy, General Manager
SPRING Technologies Inc.
One Broadway (14th Floor)
Cambridge, MA 02142
617-401-2197
sproisy@springplm.com
www.springplm.com