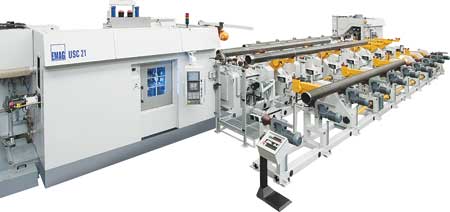
The USC series of machines from EMAG are optimized for the thread cutting of delivery pipes and casings.
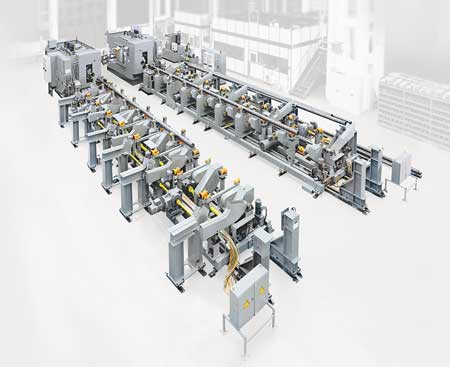
The flexible loading of the workpieces is designed specifically for the customer and is fully automated. The transport system does not need to be reset and adjusts itself to individual tasks and workpiece dimensions.
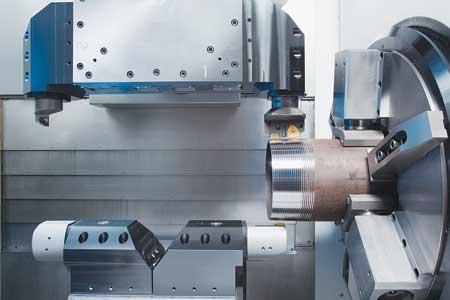
These machines are designed to handle a large amount of pipe material and are made to suit manufacturer's individual requirements. The threading process takes 12 to 20 seconds.
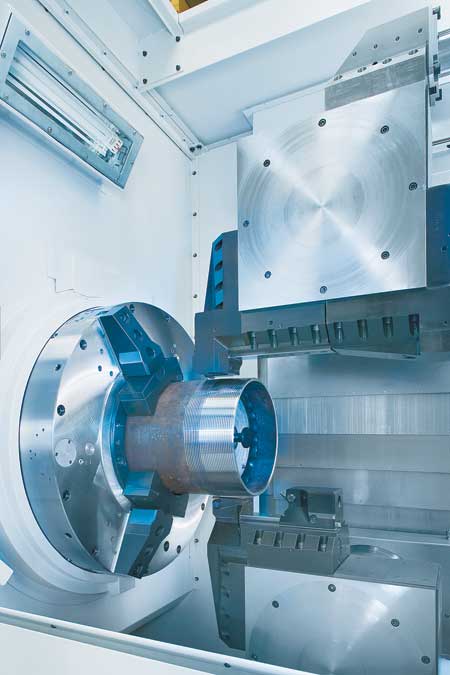
The two compound slides with 4-position table-type turrets accommodate a number of different tooling systems. The various quick-change toolholders hold tools for external and internal turning operations. The compound slides are subject to high rapid traverse speeds in X- and Z-axis and ensure idle times are kept short. The guideway system for the slide unit features pre-loaded linear roller guides for enhanced machining accuracy and high dynamics.
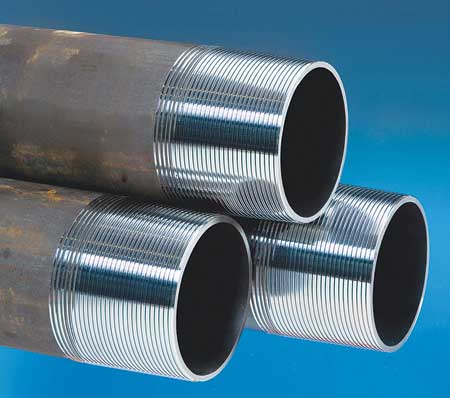
The USC series offers rigidity, preloaded linear guideways and dampening clamping systems for the precise production of thread profiles.
EMAG Leipzig Maschinenfabrik is a machine builder that specializes in machines used to manufacture pipes and casings for the oil and gas industry. "In this industry, we are talking about a gigantic production output," said Frank Schiffler, Head of Sales. "One steel mill produces up to 2 million metric tons of pipes per annum. Component quality is paramount for these because the pipe threads have to be totally leak-proof and must carry the enormous total weight of pipe and oil during the delivery. The machining centers used must ensure that the quality and efficiency of the threads produced is 100%." The USC series from EMAG is designed to meet these industry requirements.
Flexibility is important in the construction of these turning machines. Not only do the different machine sizes allow for the complete machining of different sizes of pipes with external and internal threads to API and GOST standards, they can also cut all proprietary threads. "The larger oil field technology producers have their own thread standards," said Schiffler. "We can adjust our machines perfectly to their demands." For instance, all workholding and centering equipment is configured to suit individual requirements. The same applies to all automation components. "As a result, the customer has an extremely fast production solution that automatically loads and unloads the components in 12 to 20 seconds (depending on pipe size and thread type), then carries out the 3-part threading process - from facing to chamfering and finally threadcutting," said a company spokesperson. "The output ratio therefore increases enormously, compared with that of traditional turning machines." Depending on the machine used, the max pipe diameter can be any dimension from 2-3/8" to 20".
According to EMAG, there are two important factors that must be taken into account when machining threads on delivery pipes and casings: processing quality and process integrity. To meet these requirements, EMAG offers the following on its machine tools:
- The machine base is made with Mineralit (a polymer concrete) and for stability and the vibration resistance.
- The main drive forms an integral part of the spindle unit. Its frequency-controlled, maintenance-free AC asynchronous motor provides a high torque rate, which allows for the simultaneous machining of both ends of the pipe.
- The pipes are safely clamped in front and rear chucks that - depending on workpiece requirements - can be actuated pneumatically, hydraulically or mechanically.
- The pipe ends are stabilized during the machining process by the insertion of vibration reducing mandrels for enhanced precision.
"We design complete solutions for our customers, who, in turn, benefit from the quality of the EMAG components," said Schiffler. "In addition to that, we integrate, for instance, measuring stations, crack detection equipment, embossing and plating units and, of course, a monitoring system that covers all components. At the end, what we supply is a production system that guarantees the greatest possible degree of process integrity. Of similar importance is the worldwide service presence of our specialists. Trained user and maintenance staff are available, as are a 24-hour 365-day telephone service. This ensures that possible machine downtimes are reduced to an absolute minimum."
For more information contact:
Peter Loetzner
EMAG LLC
38800 Grand River Avenue
Farmington Hills, MI 48335
248-477-7440
info@usa.emag.com
www.emag.com
Southwest
AR
Ken Pope
EMAG LLC
Mobile: 256-642-6842
615-308-7170
kpope@emag.com
NM
EMAG LLC
248-477-7440
info@usa.emag.com
TX, OK, LA
David Harris
OCTG Sales Manager
EMAG LLC
248-755-9167
dharris@emag.com
Southeast
MS, TN, AL, GA, FL, SC, NC, VA
Ken Pope
EMAG LLC
Mobile: 256-642-6842
615-308-7170
kpope@emag.com
Northeast
PA, NY
Kirk Stewart
EMAG LLC
Mobile: 248-996-4703
248-442-5960
kstewart@emag.com
ME, NH, VT, MA, RI, CT, NJ, DE, MD, WV
EMAG LLC
248-477-7440
info@usa.emag.com
Midwest
IN, OH
Kirk Stewart
EMAG LLC
Mobile: 248-996-4703
248-442-5960
kstewart@emag.com
ND, SD, NE, KS, MN, IA, MO, WI, IL
Bill Konetski
EMAG LLC
Mobile: 612-804-0857
bkonetski@emag.com
KY
Ken Pope
EMAG LLC
Mobile: 256-642-6842
615-308-7170
kpope@emag.com
MI
Rob Nash
EMAG LLC
Mobile: 248-755-4290
248-442-6569
rnash@emag.com
West
MT, WY, CO, ID, UT,
AZ, WA, OR, NV, CA
EMAG LLC
248-477-7440
info@usa.emag.com