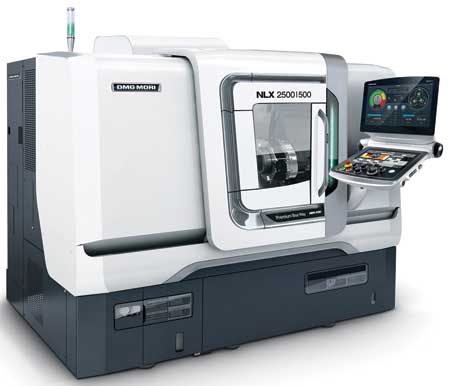
All DMG MORI machines at IMTS will feature the new common DMG MORI design.
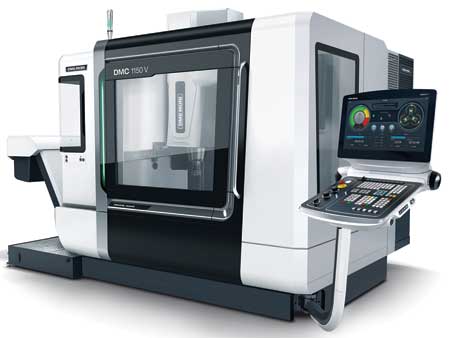
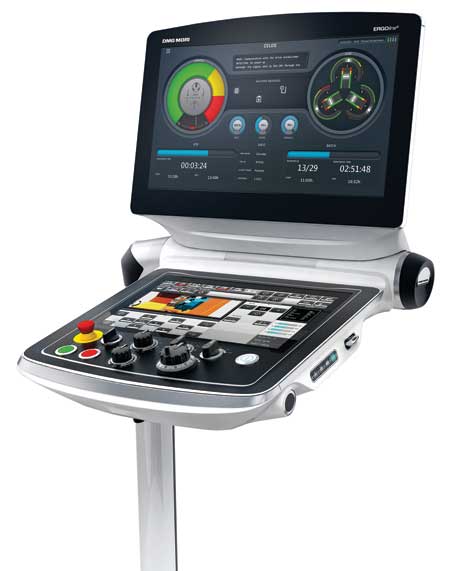
CELOS - From the idea to the finished product.
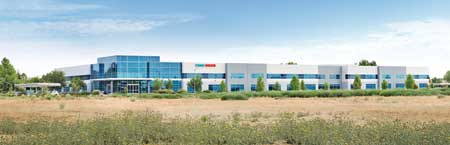
DMG MORI domestically manufactures and assembles the NHX 4000 second generation and NHX 5000 second generation, the NHX 6300 as well as the DuraVertical 5100 and DMU 50 machines.
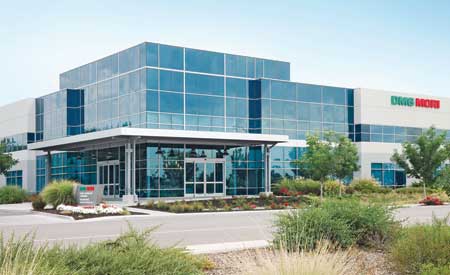
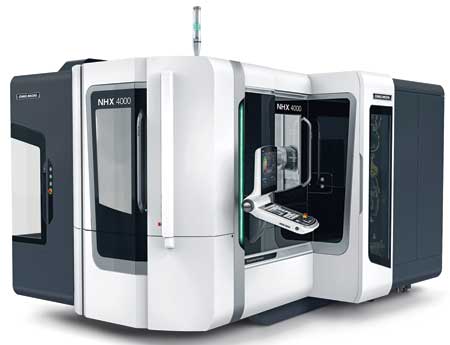
World premiere at IMTS - the new NHX 4000 second generation.
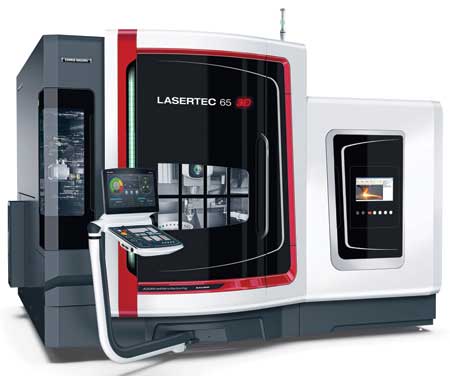
U.S premiere at IMTS - the new LASERTEC 65 3D.
DMG MORI's 32,600 sq. ft. booth will feature machines in the new common DMG MORI design. The new design offers improved functionality, and user-friendliness is provided by technological highlights including CELOS, DMG MORI's new control platform, adjustable displays for improved ergonomics, SMARTkey access for personalized operator authorization and customized access privileges to the control and machine.
A total of 23 machines will be equipped with CELOS, which offers a uniform interface for all new high-tech machines from DMG MORI. CELOS APPs provide the user with integrated and digitized management, documentation and visualization of order, process and machine data.
"CELOS is designed to simplify and accelerate the process from the idea to the finished product, and also forms the basis of paperless manufacturing," said a company spokesperson. "CELOS is as easy and intuitive to use as a smartphone, compatible with PPS and ERP systems, suitable for networking with CAD / CAM applications and ready for future CELOS APP extensions. CELOS is available for all customers in the U.S. and will be a valuable tool to boost productivity now that the North American manufacturing industry is rebounding. Additional support will come from DMG MORI's local manufacturing plant and Digital Technology Lab."
World Premieres: Second Generation NHX 4000 and NHX 5000
Manufactured and assembled domestically, DMG MORI's NHX series of high-precision, high-speed horizontal machining centers are designed for high-speed, high-rigidity and high-precision machining. The NHX series has been further improved and now includes two second generation models: the NHX 4000 and NHX 5000.
The heavy-duty horizontal machining centers are designed for machining workpieces of up to 31.4" x 39.3", with a loading capacity of up to 1,100 lbs. (NHX 5000 second generation, optionally up to 1,540 lbs). The spindle offers 15,000 RPM and power-to-torque ratio of 29.5 HP with 93.7 ft-lbs. Rapid traverse has been increased to 39.4 in/s or 63.0 in/s (optional), while the new design and the advanced controller (MAPPS V and CELOS) complement the machine's high-performance features.
The workpiece range of the NHX 4000 with 400-size pallets (15.7" x 15.7") comprises workpieces up to 24.8" in diameter and 35.4" in height (NHX 5000 second generation: 31.5" x 39.4"). The NHX 4000 features a work area of 22.0" x 22.0" x 26.0" (XYZ) and NHX 5000 is 28.7" x 28.7" x 34.6" (XYZ). Chip-to-chip time has also been improved to less than 2.4 seconds. The NHX series offers a circular accuracy of < 0.000067" with 1.3 in/s feed in X and Y as well as 3.9" radius.
U.S. Premiere: LASERTEC 65 3D
DMG MORI's hybrid technology combines subtractive machining (SM) and laser metal deposition processes for additive manufacturing (AM). The LASERTEC 65 3D is based on a DMU 65 monoBLOCK machine and has been developed by SAUER LASERTEC in Pfronten, Germany, in collaboration with DMG MORI USA. The machine is equipped with a powerful diode laser for metal deposition, while the 5-axis machine platform enables highly accurate SM operations to be carried out.
According to the company, the metal deposition process via powder nozzle is up to 10x times faster than laser sintering in a powder bed. All common metal powders can be processed, including steel, nickel and cobalt alloys, brass or titanium. Wear protection layers can also be applied on the base material.
A Focus on Automation
A dedicated area at the booth will cover all aspects of automation solutions offered by DMG MORI that are designed to improve customers' processes and increase productivity. "When DMG MORI is talking about automation, it does not stop with machine-integrated automation such as workpiece and pallet handling," said the spokesperson. "DMG MORI focuses on complete manufacturing processes and production optimization. The work therefore includes not just workpiece handling but the linking of machining centers and, if possible, the integration of secondary processes parallel to primary machining time.
"Every automation solution is based on modular components that are customized to align with customer requirements. Visitors to IMTS can experience the various solutions at the DMG MORI booth and discuss their specific requirements."
For more information contact:
DMG MORI USA
2400 Huntington Blvd.
Hoffman Estates, IL 60192
847-593-5400
www.us.dmgmori.com
IMTS 2014 Booth S-8900